SOLDADURA
localizada de las partes a unir, mediante la aplicación conveniente de calor o presión.
Puede ser con y sin aporte de material a las piezas unidas, donde el material de
aporte es de igual o diferente tipo a las partes a unir. Es importante tener en cuenta
que la soldadura cambia la estructura física de los materiales que se suelden, debido
Tipos de soldadura
La mayoría de los procesos de soldadura requieren la generación de altas
temperaturas para hacer posible la unión de los metales envueltos. El tipo de fuente
de calor, o en otros términos, la forma de producir la fusión, es básicamente lo que
describe el tipo de proceso los cuales se agrupan en tres categorías: Welding o
soldadura fuerte, Soldering y Brazing, soldaduras débiles.
Soldadura Fuerte (Welding)
Es una operación en la cual dos o más partes son unidas mediante calor o presión o
ambos efectos a la vez, obteniéndose continuidad de la naturaleza del material entre
las partes unidas. Este tipo de soldadura se puede realizar con o sin material de
aporte.
Tipos de soldadura “Welding”:
• SOLDADURA POR DIFUSION
• SOLDADURA POR FRICCION
• SOLDADURA AUTOGENA
• SOLDADURA POR HAZ DE ELECTRONES
En el laboratorio de producción encontramos varios tipos de esta clase de soldadura
como lo son: soldadura por arco eléctrico, soldadura autógena o por gas y la
soldadura por resistencia (puntos).
Soldadura Autógena o por gas
En el proceso de soldadura y corte con Gas, el principio es simple: una intensa llama
es producida por la combustión controlada de una mezcla de oxigeno y un gas
combustible. Los gases son obtenidos de fuentes o tanques separados y pasados a
través de reguladores y luego pasados a través de una antorcha en donde se
mezclan, para salir por la boquilla donde ocurre la ignición.
La intensidad de la llama depende del flujo de los gases, la proporción de la mezcla y las propiedades del gas combustible seleccionado, así como del tipo de cabeza de soldadura o boquilla. El flujo de los gases y la proporción de la mezcla son controlados por los reguladores de presión y las válvulas ubicadas en la antorcha.
![]() |
Elementos de soldadura autogena |
Las soldaduras son formadas por el cordón de metal fundido del metal base y el material de aporte (cuando se usa) que se forma con el contacto de la flama.
El material de aporte puede ser desde el mismo de las piezas a unir ó una varilla de metal con alto contenido en plata (bajo punto de fusión) usadas en la soldadura de chapas muy finas, zonas delicadas o piezas de diferentes metales.
El uso de fundentes remueve el oxido y las costras del área de soldadura y ayuda a asegurar una soldadura de calidad.
En operaciones de corte, la llama es concentrada para precalentar y mantener el metal en su temperatura de fundición, mientras que un chorro de oxigeno es dirigido al área precalentada.
Este chorro de oxigeno rápidamente oxida el metal en un camino angosto y lo expulsa, para formar una ranura.El proceso de corte con llama es el mas antiguo de todos los procedimientos de corte metálico, además el mas difundido por todo el mundo. sin embargo, hoy en día, esta siendo reemplazado por el corte por plasma.
El equipo básico necesario para efectuar las operaciones de soldadura y corte incluyen una antorcha con cabezas de soldadura (boquillas de soldadura), una extensión o accesorio para cortar, mangueras y reguladores para ambos gases, oxigeno y acetileno u otro gas combustible.
Soldadura por Arco o Eléctrica
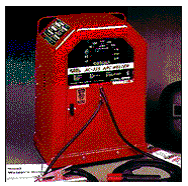
Arco Eléctrico
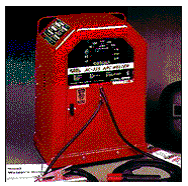
Como el nombre lo sugiere, es un
arco eléctrico que se establece entre las partes a soldar y un electrodo
metálico.
La energía eléctrica, convertida en calor, genera una temperatura en
el arco cerca de 5,500 grados centígrados (10,000 F), causando la fundición de
los metales y después la unión.
Uno de los principales problemas
en soldadura, es el comportamiento de los metales ante la combinación de los
agentes atmosféricos y los cambios en su temperatura.
El método de proteger el
metal caliente del ataque de la atmósfera (oxidación) es uno de los mayores problemas
a resolver.
Las técnicas desarrolladas van desde "Protección por
fundente" (Flux Covering), hasta la de “Protección por gas Inerte”: son
escudos protectores del oxígeno del aire.
![]() |
Soldadura arco eléctrico manual recubierto |
En algunas instancias la atmósfera
es removida completamente usando sistemas de vacío (soldadura por haz de
electrones).
Proceso:
El proceso se realiza mediante un arco eléctrico que es mantenido entre la punta de un electrodo cubierto y la pieza a trabajar.Las gotas de metal derretido son transferidas a través del arco y son convertidas en un cordón de soldadura.
Un escudo protector de gases es producido por la sublimación del material fundente que cubre el electrodo.
La escoria debe ser removida
completamente después de cada cordón.
Aplicaciones:
En 1904 Oscar Kjellberg fue el
inventor del electrodo cubierto, y con este, la invención de la soldadura de
arco.
Ahora cientos de diferentes variedades de electrodos son producidos, a
veces conteniendo aleaciones para el trabajo estructural metálico, dando fuerza
y ductilidad al cordón de soldadura.
Las labores más ligeras son efectuadas
usando potencia AC por el bajo costo de los transformadores que la producen.
En
cambio el trabajo de alta producción industrial usualmente requiere de fuentes
DC más poderosas y grandes rectificadores, para darle la polaridad exacta al
proceso.
El proceso es mayormente usado
para soldar aceros de bajo carbono en trabajos metálicos estructurales,
fabricación de barcos e industrias en general.
A pesar de lo relativamente
lento del proceso, por el recambio de electrodos y la remoción de la escoria,
se mantiene como una de las técnicas más flexibles y sus ventajas en áreas de
acceso restringido son notables.
Videos : ¿Cómo utilizar la soldadura de arco?
Parte 1
Parte 2
Soldadura por resistencia (De punto)
Se realiza por el calentamiento
que experimentan los metales debido a su resistencia al flujo de una corriente
eléctrica (efecto Joule).
Los electrodos se aplican a la superficie de las dos piezas: se colocan en una pinza a presión y se hace pasar por ellas una fuerte corriente eléctrica durante un corto lapso de tiempo.
La zona de unión de las dos piezas, como es la que mayor resistencia eléctrica ofrece, se calienta y se funde quedando pegadas en un pequeño “punto”.
Los componentes incluyen las partes de trabajo que se van a soldar (partes metálicas), dos electrodos opuestos, un medio para aplicar presión destinado a apretar las partes entre los electrodos y un transformador de corriente alterna desde el cual se aplica una corriente controlada.
Los electrodos se aplican a la superficie de las dos piezas: se colocan en una pinza a presión y se hace pasar por ellas una fuerte corriente eléctrica durante un corto lapso de tiempo.
La zona de unión de las dos piezas, como es la que mayor resistencia eléctrica ofrece, se calienta y se funde quedando pegadas en un pequeño “punto”.
Los componentes incluyen las partes de trabajo que se van a soldar (partes metálicas), dos electrodos opuestos, un medio para aplicar presión destinado a apretar las partes entre los electrodos y un transformador de corriente alterna desde el cual se aplica una corriente controlada.
La operación produce una zona de fusión entre las dos
partes, denominada un punto de soldadura.
Los
materiales usados para los electrodos consisten en dos grupos principales:
1.
Aleaciones basadas en cobre
2.
Compuestos de metales refractarios (combinación de cobre y tungsteno).
Al
igual que en la mayoría de los procesos de manufactura, las herramientas
(electrodos
permanentes para el paso de corriente) para la soldadura de puntos se desgastan
gradualmente con el uso. Cuando es posible llevarlo a cabo, los electrodos se
diseñan con canales internos para su enfriamiento con agua.
En
comparación con la soldadura con arco eléctrico, la soldadura de resistencia no
usa gases protectores, fundentes o material de aporte, y los electrodos que conducen
la corriente eléctrica para el proceso no son consumibles.
Aplicación:
La aplicación de la
soldadura de resistencia por puntos es variada:
- producción masiva de automóviles
- aparatos electrodomésticos
- muebles metálicos
- otros productos hechos a partir de láminas metálicas delgadas (±2.5mm de espesor).