Acabados Superficiales: Recubrimiento y Deposición
Limpieza
A menudo, debe controlarse acabado de superficie con el fin de aumentar la fuerza de fatiga de miembros muy estresadas que está sometido a cargar retrocesos. Una superficie lisa elimina las irregularidades agudas que son la mayor fuente potencial de grietas de fatiga.
Para partes como engranajes, control de acabado de superficie puede ser necesario Asegúrese de operaciones tranquilas. En otros casos, sin embargo, cuando una lubricación de límite existe la condición o donde superficies no sea compatibles, como en dos extremadamente superficies difíciles ejecución junta, una superficie ligeramente rugosa será generalmente prestar asistencia en lubricación.
También es necesario a fin de un grado específico de la rugosidad superficial acomodar desgaste en de ciertas partes. No alcanzar mayoría piezas móviles de nuevos una condición de lubricación completa como resultado de geometría imperfecto, ejecutando la certificación y las distorsiones térmicas. Por lo tanto, deben las superficies usar en un proceso de eliminación real de metal. El acabado de superficie debe ser un compromiso entre la rugosidad suficiente para desgaste adecuada y suficiente suavidad de vida de servicio esperado.
La consecuencia inmediata de la fabricación de una pieza es que esta sea apta en dos aspectos fundamentales que afectan a toda pieza, aislada o como parte de un conjunto.
- Su funcionamiento
- Su intercambiabilidad
Como consecuencia de ello la pieza deberá tener sus dimensiones entre límites, tolerancias dimensionales, formas, tolerancias geométricas. Además, para que su funcionamiento sea correcto debe tener definido el acabado superficial o el estado final de las distintas superficies de ella.
- Estado de las superficies
Al fabricar una pieza utilizando diferentes maquinas y útiles, por muy sofisticadas que estas sean no se puede conseguir la perfección teórica. Como consecuencia de ello se producen imperfecciones en las diferentes superficies de la pieza, las que se pueden clasificar en dos tipos.
- RUGOSIDAD: su origen son las huellas que dejan las herramientas empleadas para mecanizar o trabajar su superficie.
- ONDULACIÓN: Se produce como efecto de las holguras y desajustes que existen en las maquinas y herramientas que se emplean para trabajar su superficie.
Se tiene que tener en cuenta que este tipo de imperfecciones o irregularidades no son incompatibles y generalmente se presentan simultáneamente.
Pintura
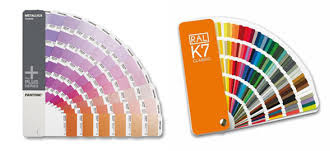
La aplicación con pincel:
Constituye el método más antiguo y su técnica es sólo sencilla desde un punto de vista aparente. La elección del pincel, en lo referente a la calidad y tamaño, debe considerar el tipo de estructura y la calidad del acabado deseado.
Las variables de calidad de un pincel son el tipo de cerda (animal, vegetal o sintética), la longitud, la forma del corte de la punta de la fibra individual y del conjunto, la densidad y las propiedades fisicomecánicas, particularmente la flexibilidad.
Los pinceles de buena calidad se pueden emplear directamente; sin embargo, en todos los casos resulta aconsejable una inmersión previa en aceite de lino crudo evitando una deformación de su extremo por acción gravitatoria. Posteriormente, se debe lavar con aguarrás mineral para eliminar el exceso de aceite; la absorción del ligante de la pintura se reduce de esta manera sensiblemente.
La selección adecuada del pincel permite cubrir con una capa, dependiendo del tipo de sustrato y su diseño, aproximadamente entre 8 y 15 metros cuadrado por hora.
Finalmente y luego de su uso, el pincel se debe limpiar con el disolvente de la pintura. Luego, se aconseja dejarlo en suspensión para evitar su deformación en el mismo solvente; el nivel no debe alcanzar la virola para no producir el ablandamiento del pegamento que fija las cerdas al mango.
La aplicación con guante:
Se emplea para el pintado de superficies irregulares, tales como cañerías y ángulos agudos, o bien difícilmente accesibles requieren la elección de otro método más conveniente que el pincel. Así, por ejemplo, puede seleccionarse un guante aplicador cuyo empleo tiene una marcada similitud con un rodillo: se ubica pintura sobre él y se desplaza posteriormente sobre la superficie a pintar.
La aplicación con rodillo:
Es un método que se emplea para pintar sobre superficies de elevado tamaño, preferentemente no muy irregulares. La selección del rodillo en lo referente a su dimensión, al material y al largo de las fibras resulta esencial para realizar una correcta y eficiente aplicación.
Los rodillos convencionales se sumergen en bandejas inclinadas a 40/45o y se desplazan varias veces por el escurridor para distribuir homogéneamente la pintura. El rendimiento en superficies grandes y lisas o al menos no muy irregulares oscila entre 20 y 50 m2 por hora para cada capa.
Generalmente se complementa con el pincel, aplicando la pintura con rodillo en las superficies lisas de grandes dimensiones y retocando con pincel los bordes, rincones, ángulos, etc. En otros casos, cuando las superficies presentan muchas irregularidades por prolongada acción del medio o bien nuevas pero con elevada rugosidad resulta aconsejable aplicar la primera capa con pincel y continuar con rodillo las restantes.
Los rodillos son diseñados para su adaptación a diversos sustratos según su forma o geometría; así por ejemplo existen rodillos para alambrados, para el interior de cañerías y para tareas específicas alimentados con aire a presión y para elevada capacidad de nivelación (acabado brillante).
La aplicación con espátula:
Se emplea para pinturas líquidas sin solvente (por ejemplo productos epoxídicos de doble envase); estos productos requieren de esta herramienta especial, de variadas dimensiones, para lograr el acceso particularmente al interior de tanques para almacenamiento de agua potable o envases de productos alimenticios.
LA PINTURA ELECTROSTÁTICA
La pintura en polvo electrostática básicamente es una
alternativa diferente para el recubrimiento
de piezas, con grandes ventajas en comparación con las alternativas existentes
en recubrimientos.
La Pintura en Polvo es una mezcla homogénea de cargas
minerales, pigmentos y resinas en forma sólida, en forma de partículas finas,
que se aplica con un equipamiento especial-pistola electrostática para polvo-en
el que se mezcla con aire y se carga eléctricamente.
Las partículas cargadas
eléctricamente se adhieren a la superficie a ser pintada, que está a tierra.
Las partículas de Pintura en Polvo que permanecen adheridas a la pieza por carga
estática son inmediatamente calentadas en un horno donde se transforman en un
revestimiento continuo.
Cuando la pintura se funde los componentes químicos, en este
caso las resinas, reaccionan entre sí formando una película. El resultado es un
revestimiento uniforme, de alta calidad, adherido a la superficie, atractivo y
durable.
Las ventajas que se tienen al implementar la pintura en
polvo electrostática se verían reflejadas en la eficiencia de aplicación, el
hecho de que no son inflamables, la reducción de área en el depósito siendo
comparativo con las mismas proporciones de pintura liquida, la reducción de
costos en la deposición de 19 los residuos generados en el proceso, tiene un
reciclaje del 95% de la pintura que no queda aplicada a la pieza, es menos
peligrosa para la salud de los operarios en comparación con la pintura liquida
y tiene una resistencia físico-química muy superior frete a impactos, rayones,
dobleces y agentes químicos.
APLICACIÓN DE LA PINTURA ELECTROSTÁTICA.
Para aplicar la pintura en polvo electrostática a una
superficie se basa en el principio de funcionamiento de un imán, en el cual dos
cargas opuestas se atraen.
La pintura es aplicada por equipos especializados para este
fin, los cuales se encargan de transportar la pintura por mangueras a través de
un sistema de vacío creado por aire comprimido a alta velocidad, hasta la
pistola de aplicación. Estas pistolas de aplicación cargan eléctricamente la
pintura con voltajes aproximados a los 90.000V y bajísimo amperaje, eliminando
así el peligro a un choque eléctrico.
Esta operación carga negativamente las partículas de la
pintura. La pieza que va a ser pintada se aterriza, con el fin de cargarse
positivamente, y así, generar la atracción de la pintura a la misma.
PROCESO DE CURADO EN LA PINTURA ELECTROSTÁTICA
El curado de la pintura electrostática sobre la pieza
aplicada también es conocido como el proceso de polimerización, y básicamente consta
de activar la reacción química del sistema de resinas por medio de calor. El
perfecto balanceo del sistema de sustratos y el período en que la temperatura
de este substrato permanece en la especificación entregada por los boletines
técnicos (específicos para cada línea de productos) determinará la perfecta
nivelación y la performance especificada para los ensayos Físicos y Químicos.
(Francescutti, 2007)
El esquema de curado hace referencia a las condiciones de
horneado de la pieza pintada con pintura en polvo, esto es, temperatura y
tiempo. Ambos parámetros son necesarios a la hora de considerar la
implementación de un horno o la reforma de uno existente. Si se quiere obtener
un pintado de las piezas satisfactorio es fundamental respetar las condiciones
de cura dadas por el fabricante de la pintura.
Para el correcto curado de estas pinturas es muy importante
mantenerse en los rangos establecidos puesto que un sobre curado de las mismas
puede traer consecuencias como cambio de color, disminución de brillo, manchado
y disminución en las propiedades mecánicas.
Bibliografía: